- May 11, 2023
- by Toby
- Calibration
When considering how to build or enhance a calibration program, there is a lot to consider. Especially when dealing with a wide range of pressure ranges – both high and low – when gas and liquid are employed in the process and as the calibration medium. The fundamental issue is always safety. The pressure range and media that are planned or present in your calibration scope are intimately connected to safety. Fortunately, there are several factors that impact the use of one media over another.
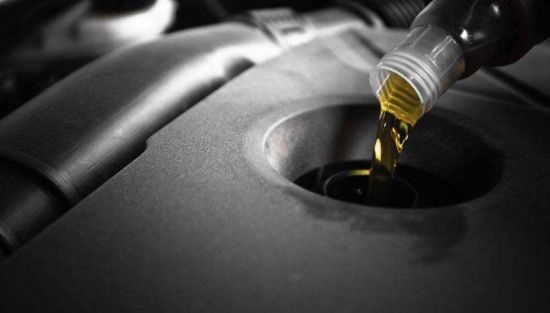
What Pressure – What Media??
The distinction between high and low pressure is purely arbitrary. High pressure often refers to pressure ranges exceeding 10,000 psi for pressure calibration components, however this is a matter of opinion and the unique operating environment. Everything is dependent on the extent of the action. If your highest range is 3,000 psi, it is your “high pressure.”
In general, pneumatic medium is utilized to calibrate the majority of pressure sensors with pressure ranges less than 1,500 psi. Some specialized applications need pneumatic media at pressures of up to 10,000 psi. As pressure rises, hydraulic fluids, most typically water or oil, become the dominating medium. It is safer to utilize hydraulic media at these higher pressure levels for the reasons explained below. The capacity to do pneumatic calibrations at pressures more than 10,000 psi exists, although it is an exception and is normally discouraged for safety concerns.
Safety
The amount of energy stored in a container filled with air or a non-volatile gas depends on the pressure and volume of the system. Because of its compressibility, pneumatic medium can store far more energy than hydraulic media. The greater the volume or pressure, the more energy is stored and potentially released in the event of a breach. A abrupt release of pressure into the environment in a high-energy pneumatic system is best defined as an explosion, and it may inflict significant harm to life and property.
Fortunately, most calibrating systems have modest volumes and hence reduced energy, but they can still inflict harm when in close proximity to a breach. The biggest worry in safety is the possibility of a high energy system containment failure. Because the volume of a typical calibration system is small, the major variable of interest is pressure. As a result, hydraulic media is often employed at pressures more than 10,000 psi. When using pneumatic media at pressures more than 10,000 psi, correctly rated fittings and tubing must be used to keep the gas contained inside the system.
Fittings
The standard industrial connectors used for connecting calibrating components containing both hydraulic and pneumatic media have a maximum pressure range of 10,000 to 15,000 psi. Fittings designed for higher pressure systems can also be utilized in low pressure systems. Elastomeric seal fittings must be compatible with the fluids utilized. Fittings developed specifically for greater pressure generally have a maximum pressure of at least 60,000 psi. Most of these are compatible with hydraulic or pneumatic fluids at their rated pressures; however, careful pressure and media selection is required.
Tubing
Depending on the wall thickness, pressure ratings for 1/4 inch OD (outside diameter) seamless stainless steel tube range from 4,000 to 10,300 psi. Fittings and tubing components often used in industrial applications or calibration labs to hold pressure and transmit fluids (both gas and liquid) have pressure ratings of up to and around 10,000 psi. Hardened stainless steel tubing can bear pressures of up to 60,000 pounds per square inch. These tube types are suitable for both gases and liquids.
Flexible nylon tubing with a working pressure rating of roughly 300 psi is often utilized in calibrating applications. Synthetic fiber reinforced flexible tubing with a value of roughly 5,800 psi is also employed. Flexible tubing is often used for pneumatic media, whereas stainless steel tubing is utilized for hydraulic media.
Compatibility
When a device is used in a process that contains hydraulic media, it is usually better to calibrate it using hydraulic fluid. If it is calibrated with air or nitrogen, it must be carefully cleaned to avoid contaminating the pressure calibrator. Alternatively, if a device under test is utilized with a gas and calibrated with a liquid, it must be cleaned before being returned to service to avoid process contamination. These factors must be considered before using a pneumatic or hydraulic medium as the calibration medium.
Pneumatic Media Types
In calibrating applications, pneumatic media are often clean, dry air or nitrogen. Other media, especially inert gasses, can be employed but are often more costly. Because of the significant danger of leakage, some inert gases, such as helium, may need to be avoided. Outside of specialist equipment and optimum calibration settings, flammable gases, such as oxygen, should be avoided, since they can induce spontaneous burning of residual oil at high pressures. The majority of other gases are rarely utilized in calibration.
Hydraulic Media Types
Hydraulic media can be deionized water or oil, depending on the equipment being tested and the calibrator used to generate the pressure. Many fluids can be utilized, but they must be compatible with the equipment under test and the calibrator. Distilled water, sebacate oil, HFE-7500, Shell Tellus-22, and other fluids are commonly used. Fluid recommendations should be provided by the calibration device’s manufacturer.
Conclusion
Many factors influence whether pneumatic or hydraulic media should be used in a calibrating application. Safety, both in terms of equipment and staff, is frequently the first priority. High-pressure pneumatic systems are more dangerous than high-pressure hydraulic systems. When calibrating devices that utilize a different medium, verified compatibility or rigorous cleaning instructions must be followed. To guarantee that all safety hazards are addressed, tubing, fittings, and seals must all be suitable with the medium being utilized.
Let Gulf Coast Manage Your Calibration Schedule.
Are you looking for calibration services, or is your equipment producing out-of-the-ordinary results? If so, you’ve come to the right place. Gulf Coast Calibration has over 40 years of expertise and has developed to become one of the Gulf Coast region finest weighing equipment and calibration firms. Our calibration services, which encompass equipment in a variety of sectors, are provided through our in-house laboratory or on-site at our clients’ facilities.
Call us to discuss your calibration, test or repair needs at:
713.944.3139.