- May 4, 2023
- by Emmanuel
- Calibration
There are inherent trade-offs between the rate at which a pressure setpoint is reached, the stability of that setpoint once reached, and the volume of the system where the pressure is being introduced when controlling pressure using a precision pressure controller in a calibration laboratory or in a production environment. This is crucial to comprehend for a production line when throughput is key. The correlations between these three factors still exist in calibration labs, where slower speeds and longer stay times are more common, but they have less impact on workflow.
For the sake of this discussion, we will concentrate on a system that includes a device that is being tested or calibrated and a precision pressure calibrating controller, such as the CPC4000. Precision pressure controllers control pressure in a volume made up of tubing, a manifold, and the transducer or transducers under test. An algorithm that reads the controller’s internal reference sensor and adjusts the regulator to add or exhaust gas to and from the system to create a steady pressure controls the stability of the pressure output.
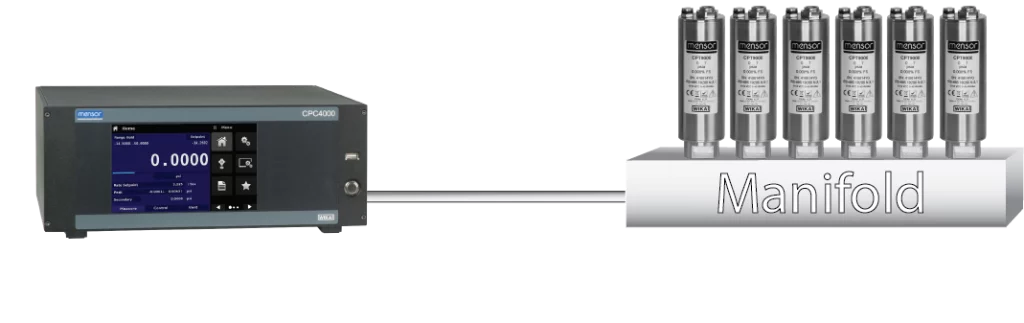
Photo Credit: mensor
In this case, the speed, stability, and volume trade-offs can have a substantial impact on the effectiveness of the entire system.
Speed Vs. Stability
Let’s start by looking at a system with a constant volume’s speed and stability. The predicted maximum pressure variation around a given point over time is the definition of the control stability parameter of a precision pressure controller. A stable situation will be shown, for instance, if the pressure stays within the CPC6050 stability window for a user-defined stable dwell duration, typically 3 or 4 seconds. This stability window is 0.003% of the active transducer range.
The time it takes to arrive at a setpoint while meeting the stability window requirements and dwell time is referred to as the speed.
Pressure calibration devices must quickly achieve a setpoint in a high-speed production testing environment in order to maximize the throughput of the component being tested. More goods can be generated the faster this is done. Testing tire pressure sensors, which are a standard feature in all new cars, is an illustration of this.
Sensors may be linked via a manifold or chamber with a constant volume and checked in groups often. In general, it is more difficult to reach a steady pressure within a short dwell time the faster a volume is filled. Momentum and thermodynamics are involved. When abruptly stopped, a large volume of gas flowing into a system will behave like a spring, causing the pressure to fluctuate about a point until the oscillation is eventually muted. Additionally, as gas moves from a low to a high pressure, it will heat up and then cool down over time, resulting in a reduction in pressure from the starting point.
By reducing the gas flow when the setpoint is reached and then adjusting the gas’s entrance and exhaust to maintain stability at that setpoint, the oscillation as previously mentioned may be managed. To prevent overshoot, the controller’s algorithm must be calibrated to recognize when to begin the throttle-down process and how to respond to slight variations in pressure near the setpoint. Every system will have a perfect set of parameters that regulate the gas’s entry and exit to operate at its fastest and most stable.
However, the faster the setpoint is attained, the more difficult it is to regulate the variation around the setpoint. The volume and geometry of the pipe and valve system, the pressure change, the temperature of the gas, and the temperature of the surrounding environment are all system variables. The operator must balance the need for speed with the need for steadiness. When the dwell period is short, the reading of the pressure standard and the reading of the equipment being tested may disagree somewhat. Given the device’s speed, stability, and precision, the operator will evaluate if the measurements are acceptable.
Speed Vs. Volume
A sensor testing system comprises a fixed volume into which pressure must be regulated. The more volume there is, the more gas is required to attain any particular setpoint. The conclusion is that larger quantities are slower to regulate than smaller volumes, which makes sense. However, bigger volumes may house a greater number of sensors, thus the slower pace may be offset by the greater number of sensors that can be evaluated simultaneously.
Volume Vs. Stability
limited variations in the amount of gas entering or departing the system create a comparatively big change in pressure in a limited volume. Small changes in the amount of gas entering or departing the system, on the other hand, will create minimal change in the system pressure in a big volume. Keeping this in mind, many applications choose a greater capacity to improve system stability.
Conclusion
It is vital to understand how speed, stability, and volume impact overall system performance. Once the aim for these variables has been set, the following step is to select the best pressure controller for the intended output.
Let Gulf Coast Manage Your Calibration Schedule.
Are you looking for calibration services, or is your equipment producing out-of-the-ordinary results? If so, you’ve come to the right place. Gulf Coast Calibration has over 40 years of expertise and has developed to become one of the Gulf Coast region finest weighing equipment and calibration firms. Our calibration services, which encompass equipment in a variety of sectors, are provided through our in-house laboratory or on-site at our clients’ facilities.
Call us to discuss your calibration, test or repair needs at:
713.944.3139.