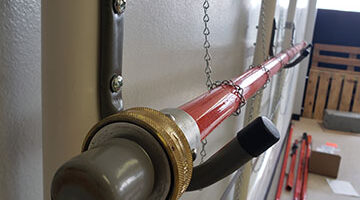

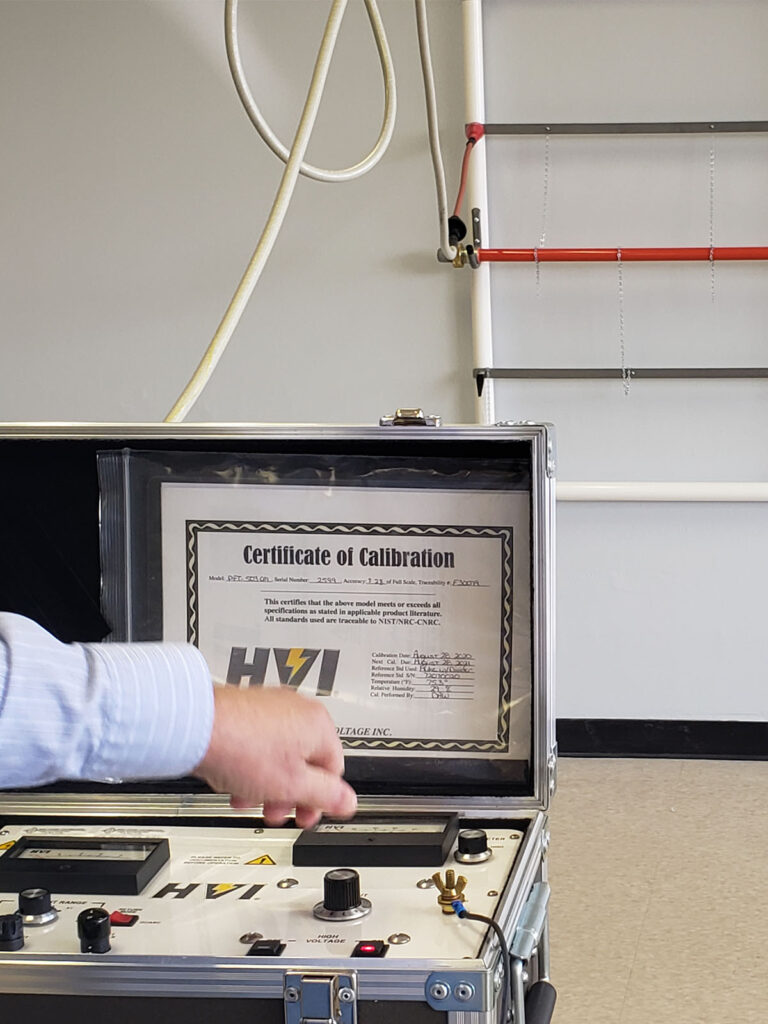
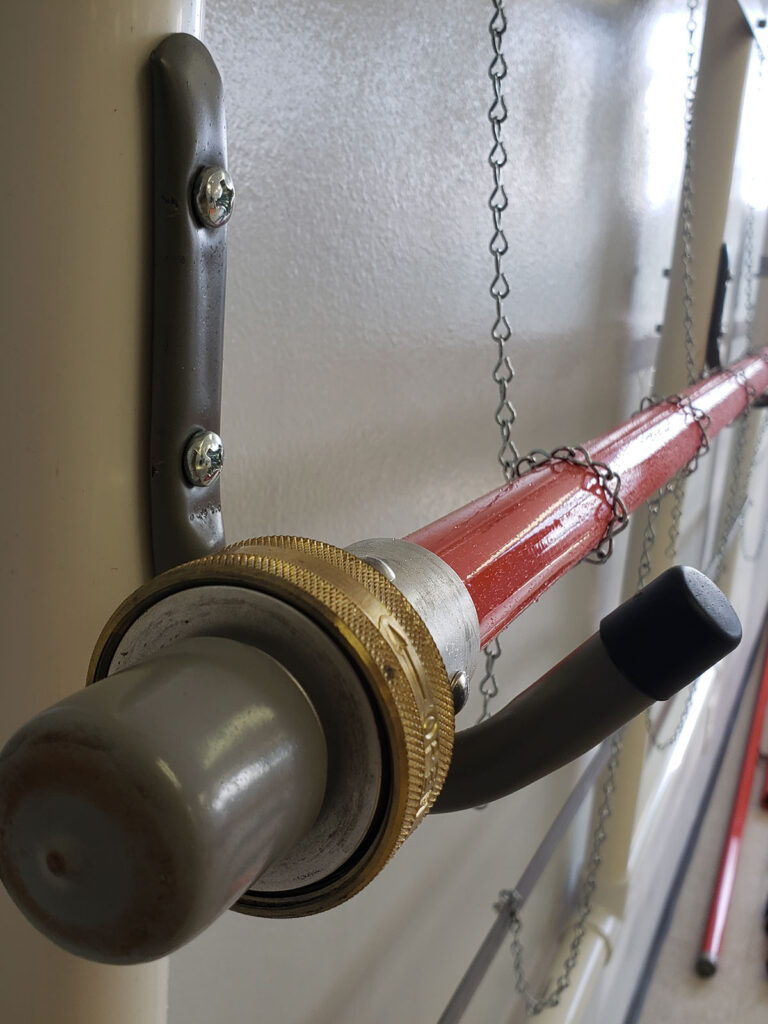
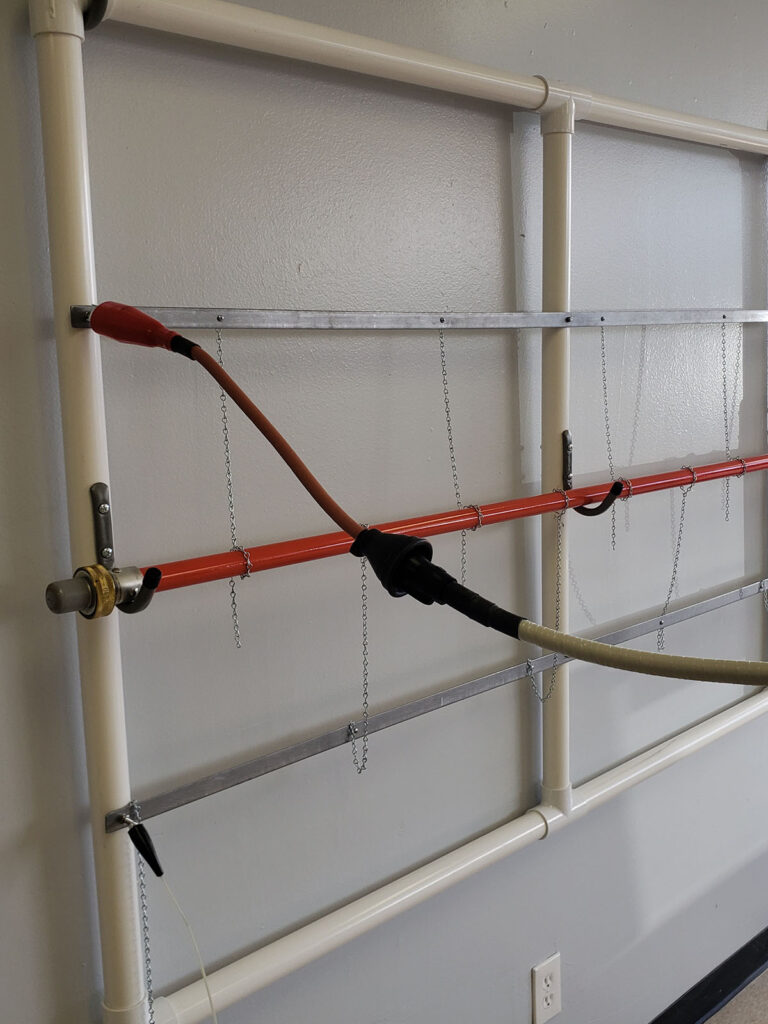
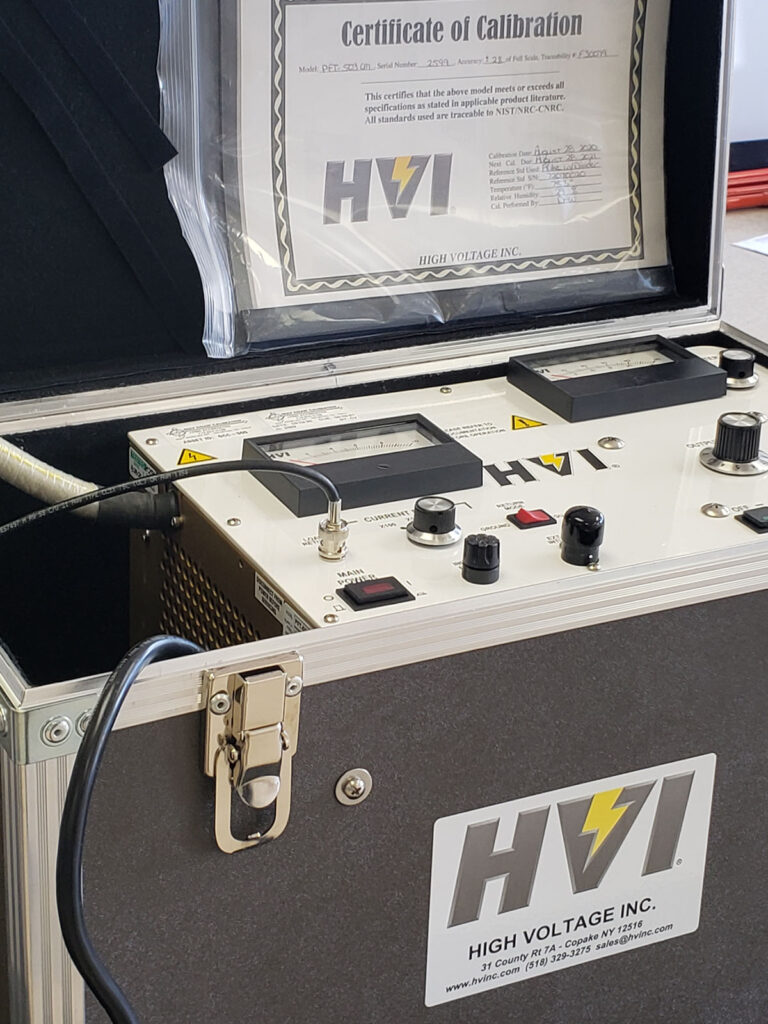
Hotline Tool Dielectric Testing, Repair, & Reconditioning Services
- Hot Sticks testing and Live Line Tools– ASTM F711, IEEE 978
- Insulating Plastic Guards– ASTM F712
- Insulated By-Pass Jumpers– ASTM F2321
- In-Service Testing for Temporary Grounding Jumpers– ASTM F2249
- Insulating Rubber & PVC Shielding– ASTM F1742
- Insulated Hand Tools– ASTM F1505
There are 2 Options to test your Line Tools:
- Lab Testing:
Send your tools to Gulf Coast Calibration to make sure they are safe and in compliance. Our shop is located at 9431 Winkler Dr Houston TX 77017. Gulf Coast Calibration Pickup & Delivery Service Available in the Houston area. We pickup and deliver tools on a regular basis, with the goal of saving our customers money. Call for details: 713.944.3139.
- Will call pick-up and drop-off is available for local customers.
- If you need to ship tools to GCC, please print off our Tools Repair Form and send in with your tools. We need your contact info to return the tools.
- Please specify how soon you need your tools back, especially if it is URGENT!
2. Onsite Testing:
We will come to your location for dielectric testing services. Our experienced technicians come to your site to perform certified testing services as part of our onsite calibration and testing services. Hot sticks testing & cable testing available, please call for details: 713.944.3139
We service the following brands:
- Cementex Tools
- Hubbell/Chance
- Hastings
- Salisbury by Honeywell
- American Hotline
- S&C Load busters and more.
Please click on the Request a Quote button below or call 713.944.3139 for all your Hot Sticks Testing needs.